半導体製造装置のメンテナンス作業中に中毒
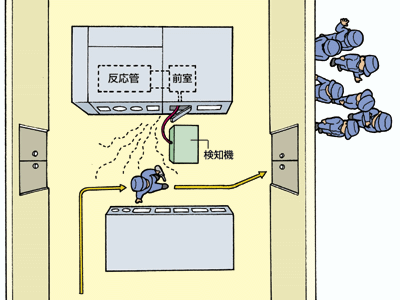
業種 | その他 | |||||
---|---|---|---|---|---|---|
事業場規模 | 5~15人 | |||||
機械設備・有害物質の種類(起因物) | 有害物 | |||||
災害の種類(事故の型) | 有害物等との接触 | |||||
被害者数 |
|
|||||
発生要因(物) | 設計不良 | |||||
発生要因(人) | 危険感覚 | |||||
発生要因(管理) | 不意の危険に対する措置の不履行 |
No.100745
発生状況
この災害は、半導体製造装置のメンテナンス作業中に発生したものである。被災者は、半導体製造装置のメンテナンスを行う会社に所属し、6か月ごとのメンテナンスや反応管の交換、清掃等の作業を行っている。
災害発生当日の午前9時30分に、メーカーの担当者4名、部品メーカーから5名、そしてメンテナンス会社から被災者と他の作業者1名が集合し、半導体メーカーが行ったベーキング作業(反応管内にガスボンベから水素を送入し、温度を上げることにより装置内の有害ガスを取り除く)および酸化作業(ボンベから酸素および窒素を送入し、反応管に付着している有害物質と反応させて酸化膜を生成させ、発散するリン等の有害物質を抑制する)の状況報告とメンテナンス作業の打ち合わせが行われた。
午前9時40分から検知作業が開始され、まずメーカーの担当者が検知器を10号機の前扉内に取り付けて検知作業を行い、他の作業者は装置の周辺でメンテナンス作業に必要な防毒マスク、工具等の準備を始めたが、検知管を取り付けるときに扉を少し開けたので燐酸化物のにんにく臭がでた。
このとき、被災者と同僚は、作業に使用する延長コードを探すため、この作業場所を離れていた。
午前9時42分にメーカーの担当者が検知器の表示で測定値150ppbを確認した。このとき他の作業者は、準備作業を終えて、装置室外で待機していた。
午前9時43分に、作業場所を離れていた被災者が検知管が取り付けられていた装置の傍を通って他の作業員と合流した。なお、被災者と行動を共にしていた同僚は別のルートで合流した。
午前9時45分に、検知管で488ppbを確認し検知作業は終了し、午前10時10分から担当者全員で検知結果を基にメンテナンス作業の開始判断の会議が行われ、測定結果は従来レベルであるが、ベーキング作業で不具合があったので当日にメンテナンス作業を行うことは中止して、再びベーキング作業を実施することを決定した。
被災者は、判定会議後、事務所で約1時間休憩していたが、体調不良なのでメーカーの産業医の診察を受け、さらに産業医の指示で大学病院で診察を受けたところ、急性薬物中毒の診断を受け4日間の入院となった。
原因
この災害の原因としては、次のようなことが考えられる。1 | 有害ガスが漏洩していたこと 半導体製造装置に残留している有害物質の検知を行うために装置の前扉を少し開け検知管を中に取り付けたが、このときに有害な物質が装置外に拡散された。 そこを被災者が他の作業者と合流するため、近道である装置室内を通行して吸入(150ppb~488ppbの間)したものと推定される。 |
2 | 作業者が防毒マスクを着用していなかったこと 検知作業においては、装置の前扉を少し開けて検知管を中に取り付けるため、短時間ではあるが扉が開放されて中の無害化されていない有害物質が漏洩する可能性があるのに、その作業に従事する者および装置室内を通過する者が防毒マスクを着用していなかった。 |
3 | 作業の指揮者が定められていなかったこと メンテナンス作業は、半導体のメーカーの担当者、部品メーカーの作業者、メンテナンス会社の作業員が共同で作業を行うが、全体の作業を指揮する者が特定されていなかった。 また、検知作業を行うときには、習慣的に装置外で待機するようになっており、室内に立ち入ることを禁止する指示、立ち入り禁止の標示措置も行われていなかった。 また、共通の作業手順書も作成されていなかった。 |
対策
同種災害の防止のためには、次のような対策の徹底が必要である。1 | 装置の扉を開放しないで有害物質の検知ができるようにすること 装置内の有害物質等の検知を扉を開けて行わなくてもできるように検知システムを自動化する等の検討を行う。 |
2 | 作業の手順書を再検討して定め関係者に徹底すること 作業の手順書について、それぞれの手順において安全衛生上配慮すべきポイントを加えたものに改定し、関係会社の作業員を含めてその内容を徹底する。 また、その日の作業の開始前に、関係作業者全員に作業手順書の再確認を行わせるとともに、KY活動等を行う。 |
3 | 有効な呼吸用保護具を使用させること 有害物質等が漏洩、拡散する場所での作業においては、有害物質に対応した有効な防毒マスクあるいはホースマスクを関係作業者の人数分をあらかじめ準備し、確実に着用させる。 また、その日の作業開始前にマスクの有効性を確認する。 |
4 | 作業の指揮者を指名し作業の指揮を行わせること 作業全体を統括指揮する者、それぞれの作業箇所で指揮する者を指名し、作業指示系統の周知、作業手順の確認、立ち入り禁止区域の設定・標示、作業の直接指揮、異常事態が発生した場合の連絡、避難の方法等を関係作業者に周知させる。 |
5 | 関係作業者に対して安全衛生教育を実施すること 半導体の製造工程で使用される物質等の中には、人体に有害なもののほか、大気と接触すると発火するもの、水やアルコールと反応して可燃性のガスを発生するもの等が少なくないので、化学物質等安全性データシート(MSDS) を収集し、関係作業者に対して十分な安全衛生教育を実施する。(安全衛生法第57条の2関連) |